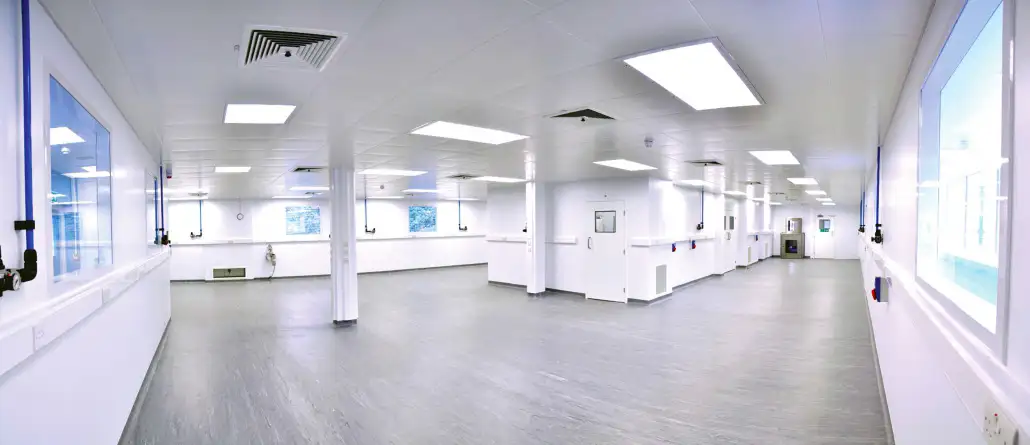
8 factors that will influence the cost of your new cleanroom
We are often asked by clients to provide a rough square metre rate for the design and construction of a new Cleanroom, and all too often we have to use that horrible phrase "that depends". Unfortunately, when it comes to providing an estimated cost for a new Cleanroom facility it really does depend and below are 8 important factors that need to be considered:
Classification - What classification of Cleanroom do you need? This is the starting point and will begin to drive the design of the HVAC systems, the type of filtration and the specification of finishes that will be required.
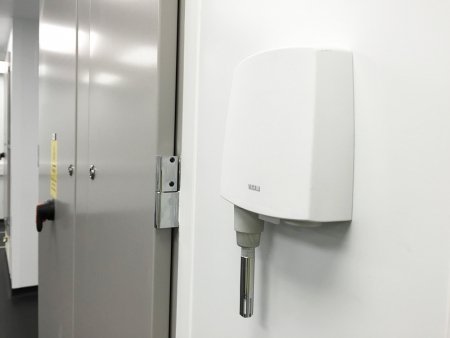
Temperature and Humidity Tolerance - Having to control temperature and humidity within the Cleanroom to tight tolerances will have a significant impact on the cost of the plant, equipment and controls required to run your Cleanroom.
Challenge your specifications. Are your temperature and humidity requirements being driven by your process, your people or your materials? Is tight control really required in all areas or just in one section; is it required at all?
Number of Occupants - People can be the biggest source of contamination within a Cleanroom, so filtration and air change rates will have to be designed accordingly. People also generate a lot of heat, especially when wearing Cleanroom clothing, so temperature and humidity control is required to ensure a pleasant and comfortable working environment.

Work Activity - What activities will be carried out in the Cleanroom? Will it be done by machines or people? Both machines and people can generate particles and a lot of heat. These factors need to be understood to enable HVAC systems to be sized and also the facility layout to be designed correctly.
Size and Complexity - It is possible for a small, high classification and complex Cleanroom to be more expensive to design and build than a larger and more straight forward facility.
If your Cleanroom requires tight humidity control, medical gases or compressed air, an Environmental Monitoring System or possibly chemical extraction, then all of these will have an impact on the construction costs.
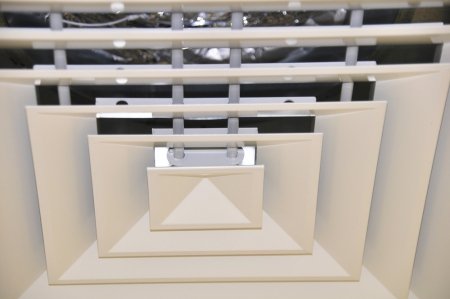
Location, Location, Location - It is not difficult to understand why a Cleanroom built on the 5th floor of a refurbished office block in the centre of London is going to be more expensive to build than the same specification facility constructed in a newly built, open plan warehouse in Kent - logistics and installation complexity. However, another factor to consider is the proximity of the HVAC plant to your Cleanroom. Where will your AHU, chillers and controls have to be located relative to your Cleanroom facility?
Availability of Services - Are the services you need to run your Cleanroom already available at site? This will again have an impact on construction cost. Are there hot and chilled water services in an existing plant room or does a packaged chiller need to be procured? Are existing compressed air system, or medical gas lines, available to be tapped into or are completely new systems, compressors and associated equipment required?
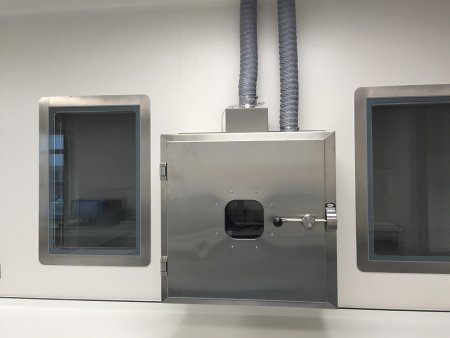
Facility Life Expectancy - Ultimately this comes down to Construction Cost vs Running Cost. Is the cleanroom to be used for 5,10 or 20yrs? With a longer life requirement for the facility, materials used and solutions provided will differ.
A simple example would be that of in-line duct heater batteries. The procurement and installation cost of an electric heater battery will be significantly less than that of an hot water coil, which will need piping, control valves and complex commissioning. However, if there is an existing hot water system on site than the running cost of the hot water coil will be significantly less than that of the electric battery over the life of the facility.
Ultimately we would always recommend that the first step is to develop a suitable User Requirement Specification which will help identify the requirements for your facility. Considering the impact 8 factors will be a good starting point for your Cleanroom construction.
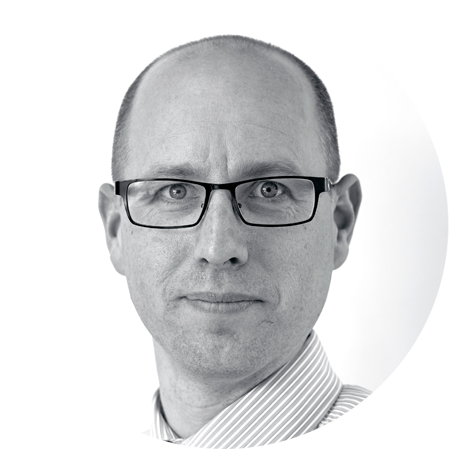
Jason Harvey
Experienced Project Manager with a demonstrated history of working in the construction and facilities services industry. Strong program and project management professional, skilled in Process Improvement, Value Stream Mapping, Decision-Making, and Quality Management. With a BEng (Hons) focused in Manufacturing Engineering and Management from Loughborough University.